How to set up your next mass timber construction project for success
XL Construction co-founder Dave Beck shares important preconstruction steps for designing and building mass timber buildings.
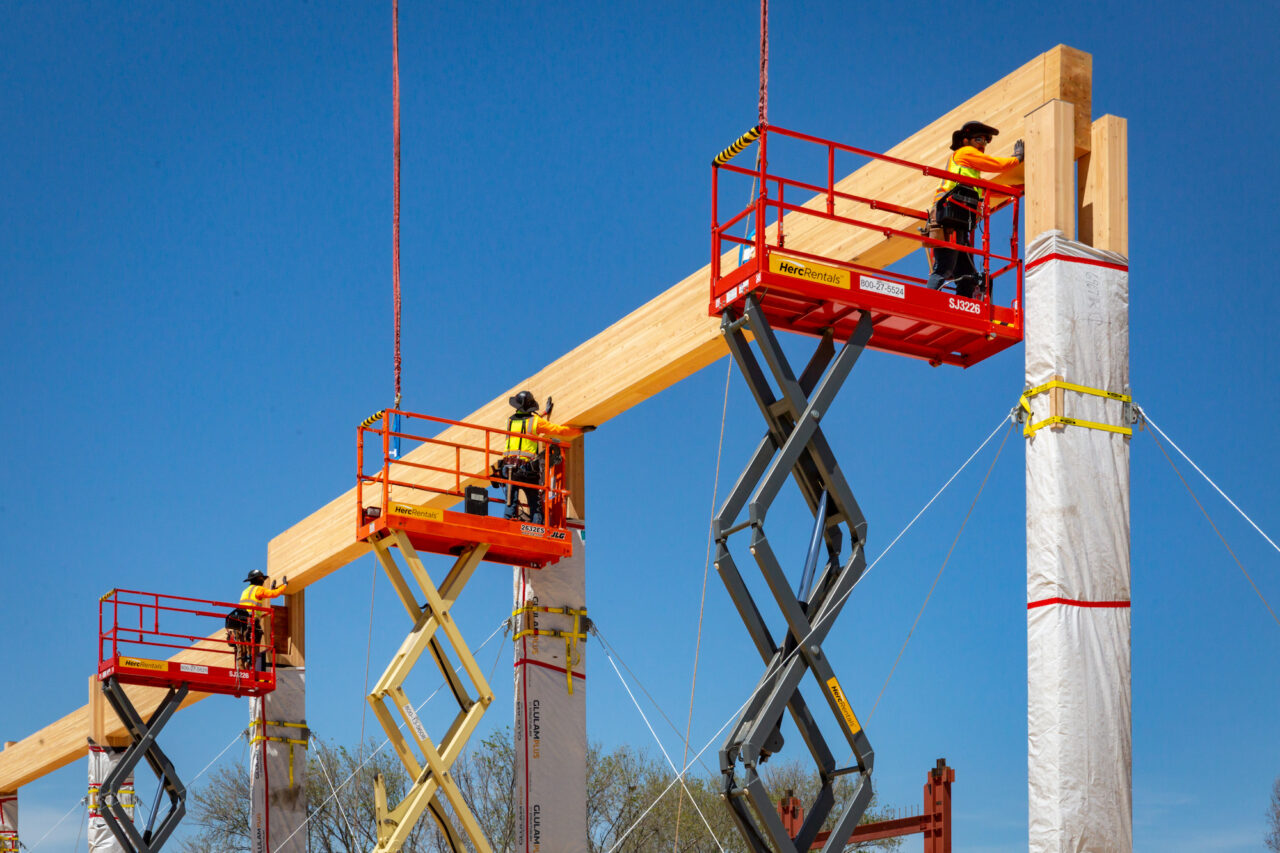
Mass timber construction, which uses various forms of wood products including glue-laminated columns and beams and cross laminated (CLT) panels instead of more traditional steel and concrete materials, has been used for many years in Europe. In the United States, this construction approach is fast gaining traction. In 2013, there were only 26 mass timber buildings. Today, there are some 1,300 either constructed or in the works according to WoodWorks, a construction industry group.
The most common mass timber typology consists of glue-laminated (glulam) beams and columns with a cross-laminated timber (CLT) floor and roof decks. However, laminated veneer lumber (LVL), nail-laminated timber (NLT), and dowel-laminated timber (DLT) can also be brought into the mix.
Each of these materials offer several key advantages that lend to their increasing popularity. The biggest draws are the beauty and health promoting biophilic and sustainable designs of the resulting spaces. Mass timber provides great carbon storage benefits—a single five-story mass timber building cuts emissions of carbon dioxide by levels equivalent to the removal of up to 600 cars from the road for a year.
From a building standpoint, mass timber rivals traditional steel and concrete building materials in durability, seismic performance, and fire resistance, while being lighter in weight and resulting in less costly foundations. Additionally, because mass timber components are machined to a high precision (+/- 1mm), the installation on site is rapid, less noisy, and utilizes a smaller installation team than alternative materials.
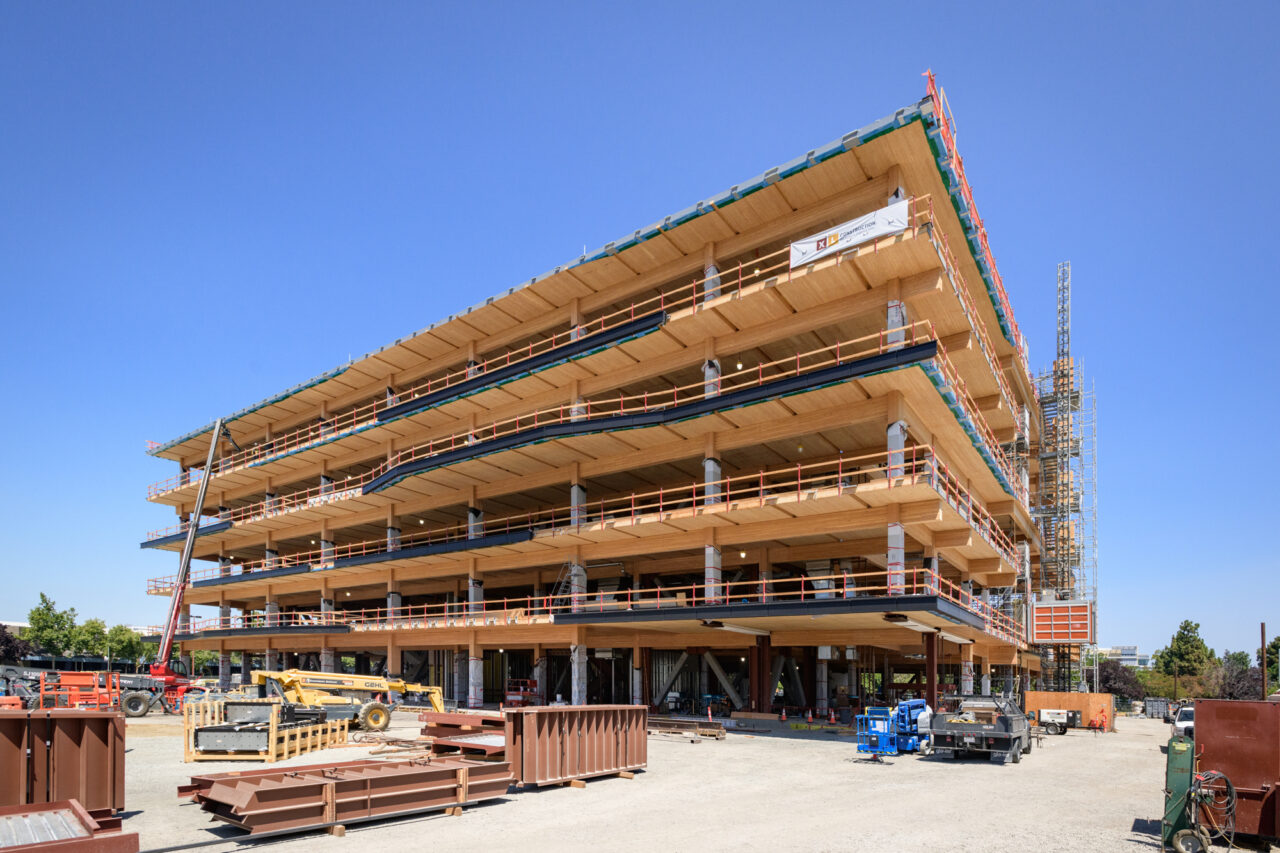
A mass timber office building under construction in Sunnyvale, Calif. Photo: George Baker, Golden State Photographic
Mass timber is scoring high marks with developers seeking buildings that they can fill faster and command higher rents, as well as with companies in competitive industries that see a “better” building as a way to attract, retain, and support their best employees.
While you may be considering mass timber for an upcoming project, it is important to be cognizant of the differences between mass timber and traditional construction materials and best practices for ensuring the success of your project. In this article, I will go over important preconstruction steps that will strengthen any mass timber project and point you in the right direction.
Get Your Team Together Early and Efficiently
Mass timber has two key differentiators from traditional materials that drive fundamentally different design and procurement processes. First, mass timber is intended to be exposed, so the structure itself should be beautiful, elegant, and consistent.
Second, the procurement of a mass timber building is quite different than a concrete or steel building, as there are many individual suppliers and subcontractors involved. Typically, the mass timber supplier doesn’t provide all of these services. These services include:
- the design for manufacturing of the glulam product and CLT products
- erection engineering design
- 3D modeling of the erection plan to work thru erection sequence
- shipping and storing of the mass timber material
- shoring of the timber product to limit deflection and support cantilever designs.
Among the many early design decisions and considerations that need to be reconciled for a successful mass timber project are:
- determining construction type
- fire-resistance ratings
- member sizes
- grids and spans
- exposed timber (where and how much)
- MEP layout (and how systems are routed through the structure)
- acoustics
- façade strategy
- concealed spaces
- connections
- penetrations.
Project-specific factors to be taken into consideration, which influence how these early decisions are made, include site size, orientation, zoning and cost, as well as building size, occupancy, layout, floor-to-floor heights, aesthetics, and sustainability goals. These factors will also dictate resulting code options and design implications.
A critical preconstruction step is to allow adequate time for the creation, review, and approval of a highly detailed 3D manufacturing model. It is more cost-effective to resolve issues before construction begins than in the field. Think of taking the “measure twice, cut once” ethos to a more sophisticated level. For example, it should be the team’s goal to have 95% of penetrations made by the manufacturer on a CNC machine. This is crucial, as a penetration that may be a matter of minutes of machining at virtually no cost in manufacturing may take an hour if drilled on the jobsite.
Securing and Handling Mass Timber components
Mass timber procurement is fundamentally different from that required for conventional construction materials. While steel, concrete, and light-framed wood construction use largely commodity materials, each mass timber manufacturer has unique panel sizes, thicknesses, and grades.
Additionally, manufacturers in different regions utilize different wood species (Douglas Fir and Spruce/Pine/Fir in the Pacific Northwest; Black Spruce in Eastern Canada; Southern Yellow Pine in the Southeast; and various species from European suppliers), so the desired aesthetic may drive manufacturer selection. For these reasons, we suggest that the manufacturer be brought in on a design assist role at the end of the concept design phase.
Another key factor is the limited number of mass timber manufacturers and their capacity. The mass timber industry is not yet mature in the U.S., so mass timber manufacturers can be booked for months or even years in advance due to the growing popularity of these projects. Beyond the mass timber itself, many of the long screws and hardware required are European-sourced and can entail significant lead times. Consulting and bringing on the manufacturers of these materials early will allow you to book production slots concurrent with design development to avoid project delays.
In assessing your project, you will need to determine whether you have the space on site to store the mass timber and related hardware materials. If you don’t, you will need to make arrangements for a staging yard and coordinate a “just in time” delivery schedule for the jobsite.
With steel, most fabricators are close by, and they can ship materials that can be craned directly from the truck. This is far less feasible for mass timber, where the suppliers are typically much further away, which can often extend delivery times. In addition, mass timber elements are bulkier, and you are less able to effectively package them for installation directly from the truck.
The arrangement of a staging yard not only provides additional space to store materials, but it also enables more flexibility in receiving mass timber and other materials from the manufacturer. This is important as the manufacture of mass timber products often takes three-to-four times longer than the installation, resulting in the need to collect and hold these materials in advance. It also gives you the peace of mind before construction begins of being able to confirm all materials are in the yard and checked for quality, as well as the opportunity to pre-install any hardware or screws that could not be put in place by the mass timber manufacturer.
Timing is Everything with mass timber construction
To achieve the best results with mass timber projects, it is important to not only design and plan well, but to do so early. This includes the procurement of sometimes hard-to-obtain mass timber and other materials. You will want to let your project owners know that shifting the preplanning, coordination, and decision-making to an earlier stage in the project does not increase the fees associated with design and preconstruction, but rather shifts the timing of the costs within the overall project schedule.
What you need to impress upon them is that this extra early effort will more likely result in a project that not only meets but exceeds their goals.
About the Author
After working in the construction business for many years, Dave Beck co-founded XL Construction with Eric Raff in 1992. In founding the company, their foremost mission was to excel in each project they executed and deliver complete customer satisfaction. XL has never wavered from that mission. It supports each project with a team of experts, ensuring that every project is done the “XL Way”: with consistency, high quality, and attention to meeting customer needs.
As Executive Vice President, Beck manages all construction field activities provided by XL Construction. Clients frequently point out that Dave personifies the company – he is easy to work with, is in constant pursuit of field excellence, and is known for his creative thinking.
He obtained a B.S. degree in Construction Management from California Polytechnic State University in San Luis Obispo, California.
Source: BuildingDesign+Construction
Keep up to date with our latest news and industry insights.
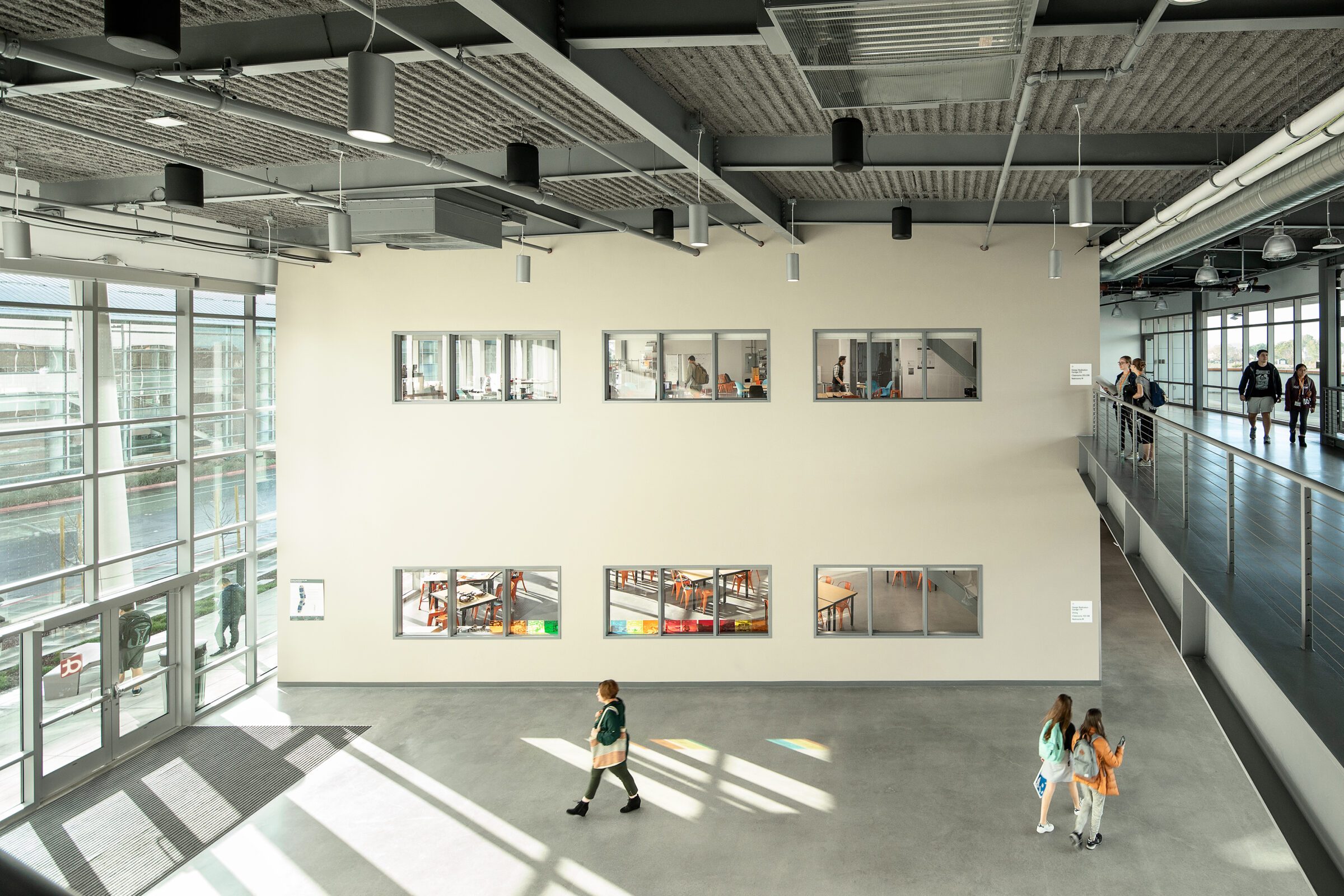