4 Key Lessons from a Mass Timber Disassembly
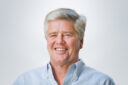
Uncover the challenges and lessons learned from mass timber building disassembly and considerations for future design and construction.
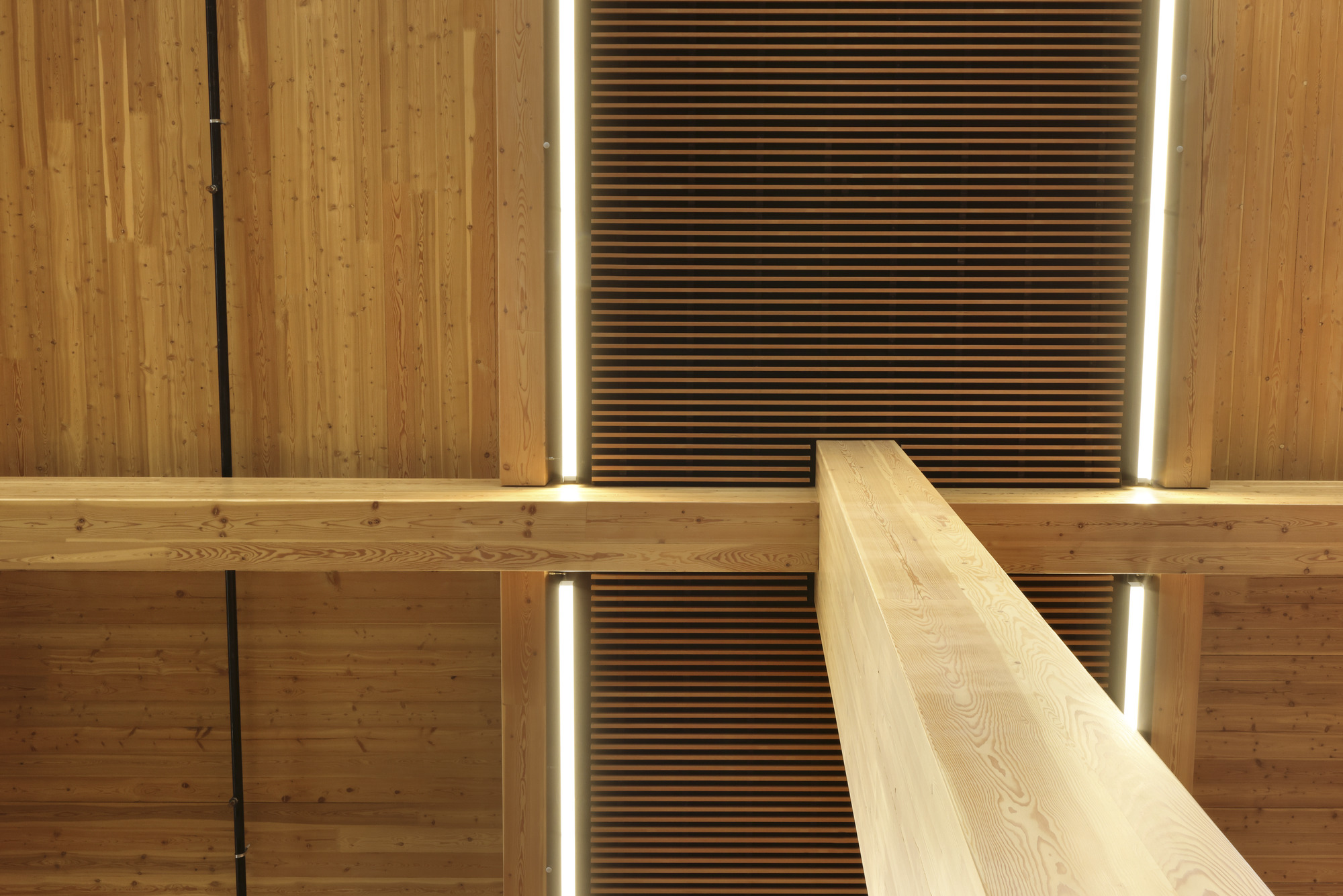
Beautiful, elegant, and sustainable—mass timber is rapidly gaining favor among developers aiming to construct faster and create stunning spaces which can command higher rents.
As a newer structural solution, mass timber combines aesthetics and performance, which offers a compelling alternative to traditional construction methods. It is and will be instrumental in achieving local and national net zero carbon goals and appeals to companies in competitive industries that view sustainable building design as key to attracting, retaining, and nurturing their top talent.
The Practicality of Reuse
Mass timber is composed of layers of wood bonded together for strength. The wood sequesters, in other words traps, carbon from the atmosphere, which stays there throughout the life of a building and potentially beyond. In theory, mass timber can be reused in a new structure after disassembly, extending the length of time in which carbon is sequestered.
Most mass timber buildings in the US were built within the last 10 years. With an anticipated life span of 50 years or more, there are limited opportunities to learn from mass timber building disassembly in the US and fully understand the practicality for its potential reuse. In 2024, XL Construction had a unique opportunity to disassemble a mass timber structure and did so with keen attention to factors that could impact the reuse of the mass timber members.
Opportunity for Disassembly and Investigation
During the development of a leading tech company’s first mass timber project, XL Construction’s design-build team constructed a full-scale, two-story, two-bay mock-up. The building served as a tool to test various mass timber connections and evaluate aesthetic options to work toward the final design and construction approach for the main building. It also served to inform jurisdictions having authority on the alternate means and methods and special inspection process required for a mass timber structure.
After the project team completed the construction of the actual five-story project, the mock-up was to be removed. Together with our client, Atelier Jones, and the University of Washington, our team posed several questions: If a mass timber building is disassembled, what can truly be salvaged? How many of the timber members can be reused, and how do the connection details impact this potential?
Our disassembly and investigation aimed to maximize reuse of materials for a future project and understand factors limiting reuse. This reflection will serve to inform the design and construction of mass timber buildings and will shape how we approach disassembly of future structures. Our findings revealed four key lessons.
Lesson 1: Understanding, in detail, how the building was erected can make disassembly more efficient.
Although the same erection company, Elevated Construction Services, led both the installation and disassembly of the mock-up and had access to the original structural and erection drawings, there were still several unknowns that posed challenges for the disassembly effort.
As expected, the erection crew installed the screws based upon the structural drawings. During disassembly however, we found extra undocumented screws that installers added during assembly as either a temporary erection aid or to replace broken screws. Without knowing where these occurred, or having a device to easily detect these screws, it was challenging to locate and remove all of them. This added an unexpected layer of difficulty.
Additionally, as certain mass timber cantilevered members became unstable during disassembly, it became clear that installers used erection aids, such as temporary shoring, for stability during erection. When instability occurred during disassembly, the team halted work to secure the structure and adjust their approach before continuing.
These experiences highlighted the difference between what was shown in the construction drawings, and what was actually built. It is important for the construction team to document minor changes, even if temporary in nature, to make future disassembly more efficient.
Lesson 2: Considerations for future screw design and placement can result in more effective screw removal and increased reusability of material.
Another major challenge was that screws placed during assembly were not designed for installation and removal. The main challenge involved the removal of long screws—some as long as twenty-four inches—that were driven into the structure at a 45-degree angle. Installers used these screws to connect cross-laminated timber (CLT) panels to the glulam beams below. We found that many of the screws either had their cylindrical heads stripped out or broke off after only extracting them a short distance. The disassembly crew, to expose portions of the broken screws, had to force the CLT panels away from the glulam beams using hydraulic jacks. Once this was done, portions of the remaining screw could be exposed and then cut releasing the panels from the beams. This action damaged portions of the top lamination of some of the glulam beams.
Considerations for future screw design and placement might include rethinking the use of angled screws, pre-drilling holes, or exploring larger, stronger alternate screws. For example, switching the head design of the screw from an inserted drive to an external socket could prevent the stripping out of the screw heads.
Lesson 3: Removing concrete from composite decks can cause damage to screws, making removal much more difficult.
The structure utilized a composite concrete and CLT deck design. Builders bonded these two different materials together using HBV metal mesh that was epoxied into the wood CLT panels and used screws, that were installed at an angle and left above the surface of the panel, which bonded to the concrete topping slab. The heavily reinforced concrete topping slabs were placed above the HBV mesh to create the composite timber concrete deck.
In the process of saw-cutting the topping slab and chipping out the concrete, heads of many screws that were not flush with the wood CLT panels were damaged, making them harder to remove. Breaking up the heavily reinforced concrete topping slab was much more difficult than anticipated and this process minimally damaged some of the HBV mesh. Fortunately, we believe the mesh can be straightened for future reuse.
Lesson 4: Base plates designed to accommodate pneumatic tools can make disassembly easier.
On this project, builders attached steel base plates to the bottom of glulam columns and anchor bolts secured them in place. Because the plates were fabricated slightly smaller than the columns themselves, the anchor bolts were positioned beneath the glulam columns, blocking access to the anchor bolt nuts. This made it impossible to use impact wrenches for removal. Additionally, concrete slurry had bonded to the exposed bolt threads, making it much harder to remove the nuts with only hand tools.
In the future, if larger baseplates were installed, there would be enough space to use pneumatic tools during disassembly, adding significant efficiency and optimizing reuse of materials.
Our Conclusion – Beyond the Build
Despite the challenges XL encountered, over 98% of the timber disassembled from this mock-up is currently stored and awaiting reuse. We learned that the design and application of screws, base plates, and composite bonding will impact the cost, ease of disassembly, and overall reusability of material for future builds. We open the floor for builders and designers to consider and assess structural design solutions for future mass timber buildings that allow for easier disassembly, resulting in improved reusability. Understanding this will be a critical step forward for future design and construction of mass timber buildings.
We build to improve lives. Learn more about mass timber with XL today.
Keep up to date with our latest news and industry insights.
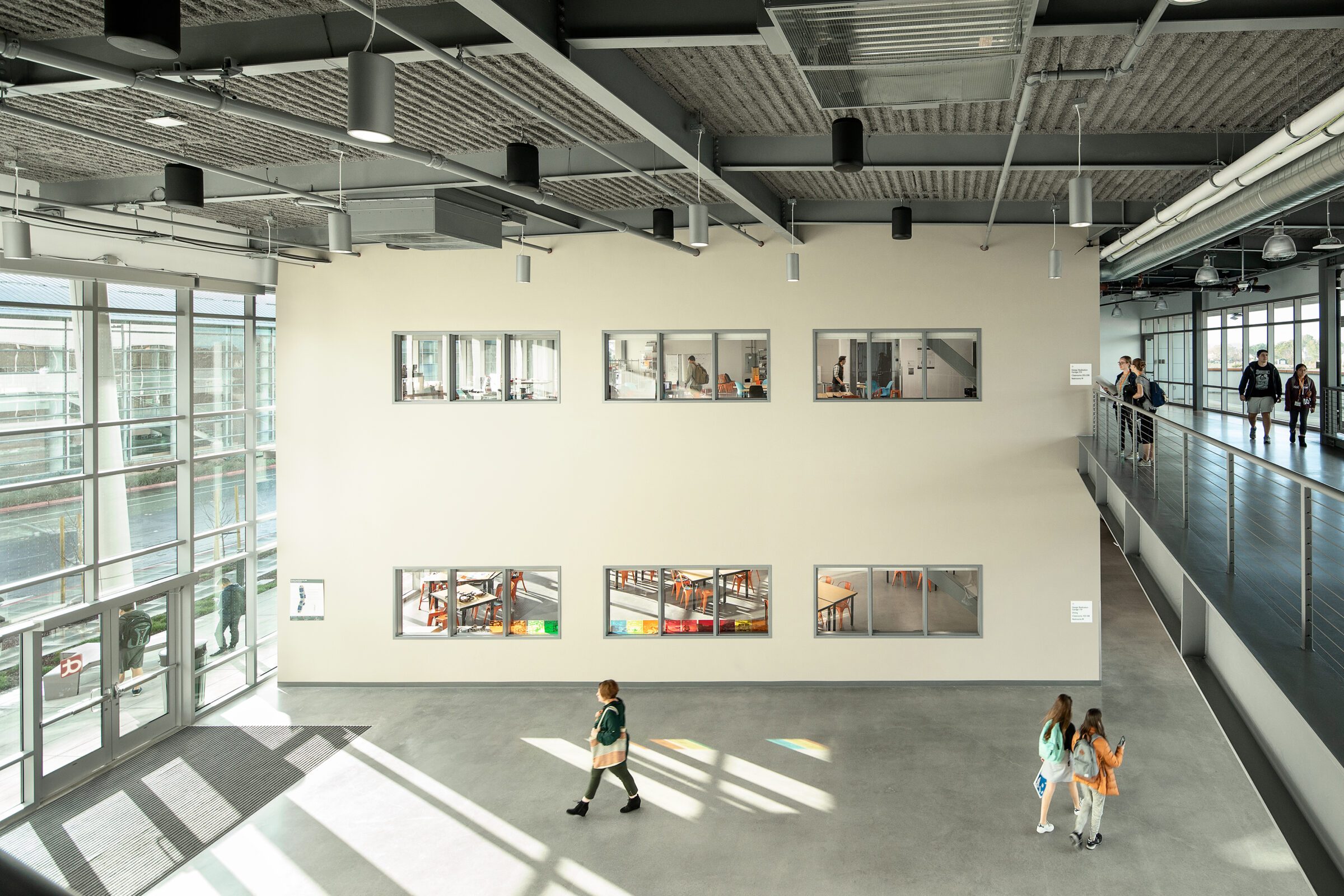