Panelists offer insight into mass timber for newcomers
An International Mass Timber Conference panel discussion about cost planning featured, from left, Dave Beck of XL Construction, Nick Milestone of Mercer Mass Timber, moderator Sam Rodriguez of Mill Creek Residential Trust, and Sebastian Popp of KLH US Holding Corp. (Hilary Dorsey/DJC)
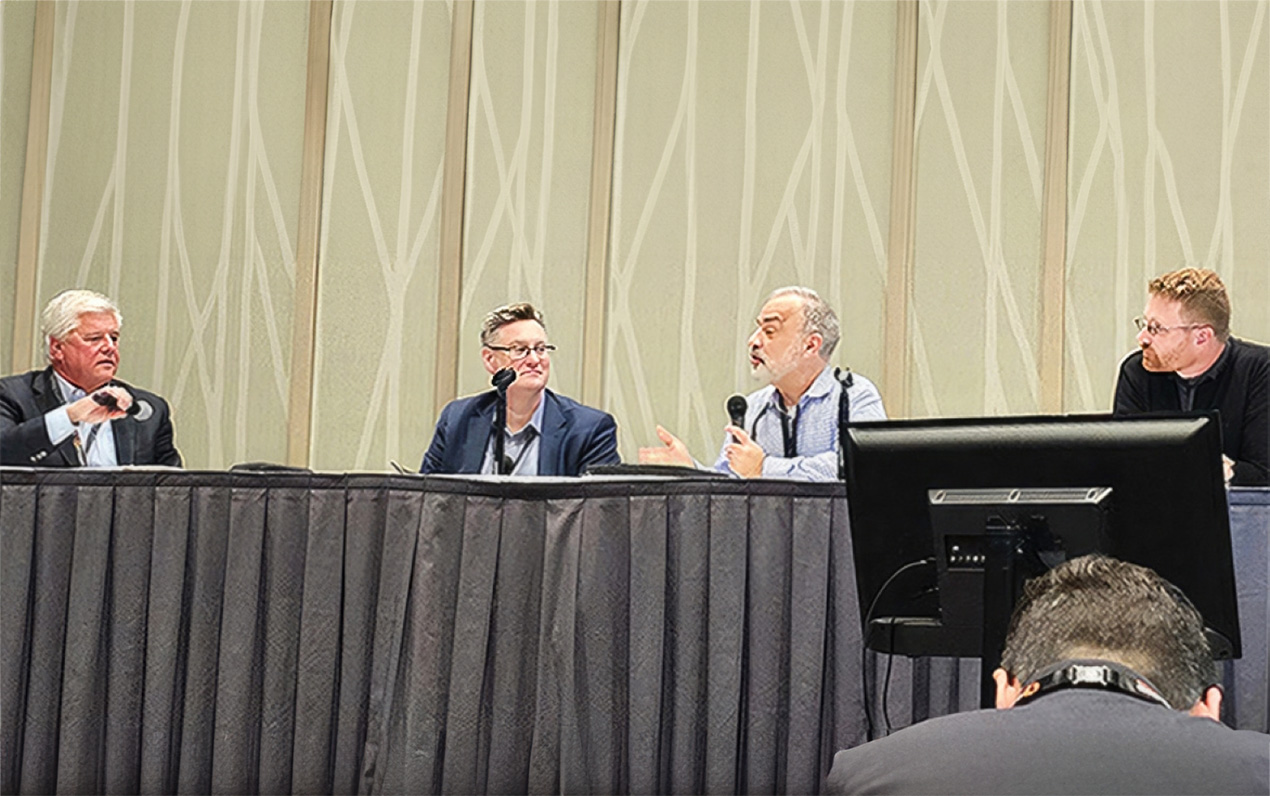
At a roundtable discussion at the International Mass Timber Conference at the Oregon Convention Center last week, panelists sought to inform building industry professionals unfamiliar with mass timber of possible obstacles to project success and how they can be addressed.
“Price Transparency, Volatility and Stability: Insights on Cost Planning” included representatives of international and North America-based manufacturers as well as a construction firm that specializes in building with mass timber. Panelists included Nick Milestone, vice president of projects and construction for Mercer Mass Timber (headquartered in Vancouver, British Columbia); Sebastian Popp, technical director for KLH US Holding Corp. (of Portland); and Dave Beck, executive vice president of XL Construction (headquartered in Milpitas, California). The discussion was moderated by Sam Rodriguez of Mill Creek Residential Trust, which has not used mass timber yet.
In an interview after the session, Arnie Didier, chief operating officer of the International Mass Timber Conference, said that when the event began several years ago, people were talking about the costs but did not really know about cross-laminated timber. Today, developers and contractors are sharing ideas, he said.
What they’re sharing is if there are ways to do things differently to contain costs and make it more attractive,
Didier said.
During the session, Milestone said mass timber is part of the solution but not entirely, because steel and concrete still have a place in projects. But mass timber can accelerate construction and reduce the number of workers on a job site, he said. Projects made of mass timber can be built 20 percent quicker and 11 percent cheaper than those with traditional materials such as steel, he estimated.
XL Construction uses its concept-level drawings to bid for a mass timber manufacturer and supplier early in the process, Beck said. Mechanical, electrical, and plumbing subcontractors and façade subs need to be involved in how buildings are designed, he added.
Although KLH sources materials from Europe, transportation and supply chain issues are minimal because vessels carry routine shipments on constant travel routes, Popp said. The firm also always has a plan B in mind if something arises, he added. These days, KLH ensures materials arrive ahead of the construction schedule. To reduce carbon emissions, the company tries to keep truck deliveries to a minimum and rely on trains instead, he said.
When it comes to selecting a project team for a mass-timber project, Beck suggested choosing an architect or structural engineer who is familiar with mass timber.
Insurance companies say mass-timber construction is a risky exercise, Popp said. It is important for project teams to find the right brokers and insurance companies early in the process. Typically, mass-timber projects have very few incidents or accidents, he added.
Insurance companies are worried about how timber is stored and protected, Beck said. When wet weather becomes an issue for a mass-timber project, he added, the team manages water mitigation during construction.
To help keep costs down, clients should engage early with manufacturers and reach out to them directly, the panelists said. Beck encouraged teams to engage manufacturers in the design process. Manufacturers’ windows are critical and should not be altered, he added.
Beck also called for more dialogue around carbon. While mass-timber buildings still have steel cores for seismic resilience, they are reducing the carbon footprint of the company’s projects by 65-70 percent, he said.
I would love to see jurisdictions provide benefits to developers for doing a more sustainable, a more carbon-friendly solution,
Beck said.
A developer or general contractor that hasn’t worked with mass timber yet ought to seek someone who has, Didier said, especially now that people are willing to share more information than in the past. If possible, he added, contractors and developers should ask for help from someone experienced, such as an installer. The increasing numbers of installation companies coming online are a game changer for the industry, he said.
A lot of companies are learning those skill sets and tackling work in-house, Didier said.
The big buzz out there is self-performed work,
he said.
That essentially is you hire your own staff to do it. Skanska is a perfect example of that on the building (the Center for Deaf and Hard of Hearing Youth) they did in Vancouver (Washington). They’re self-performing that job, which is not an easy thing to do, but it helps them control the timing of the project.
Source: DJC Oregon
Keep up to date with our latest news and industry insights.
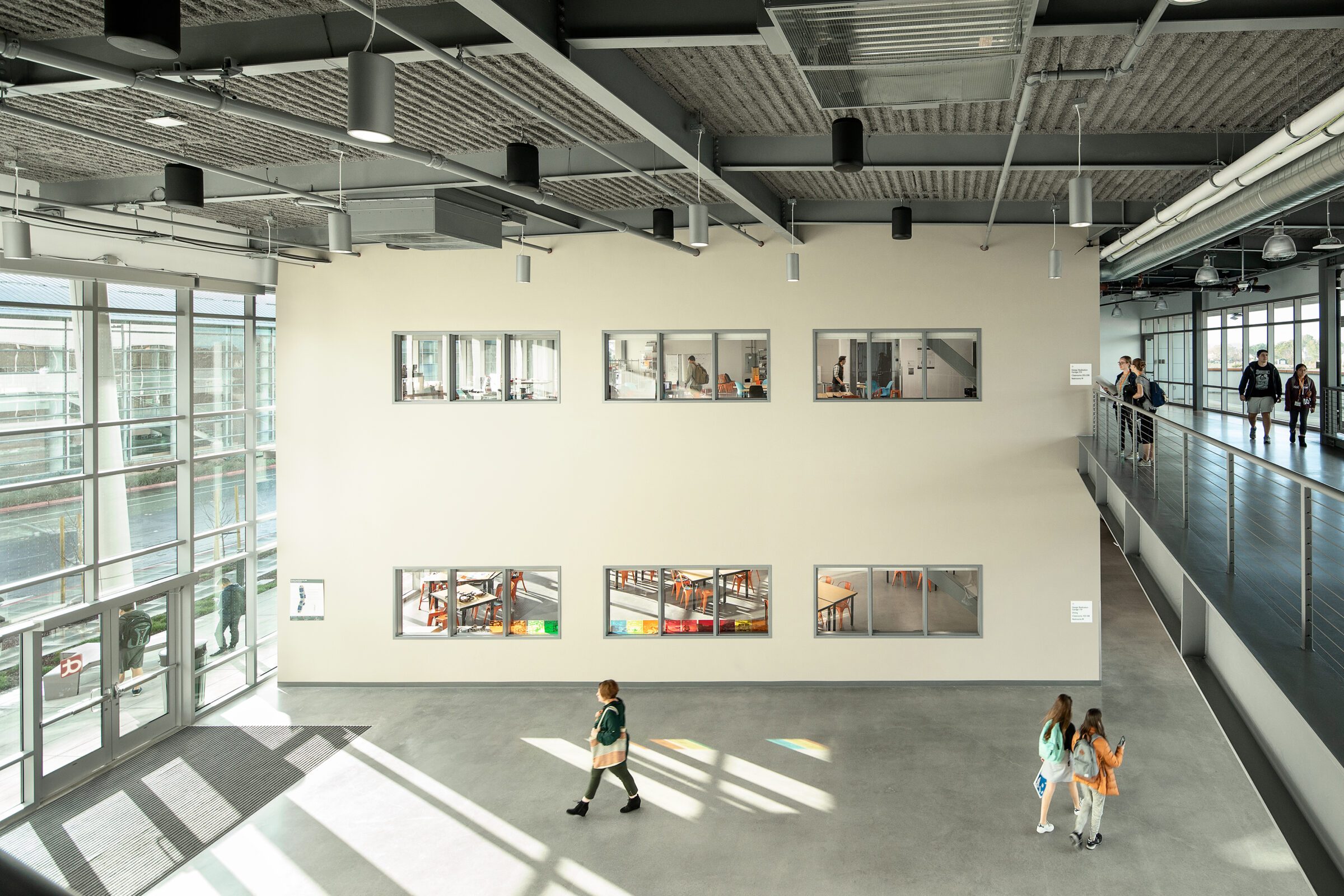